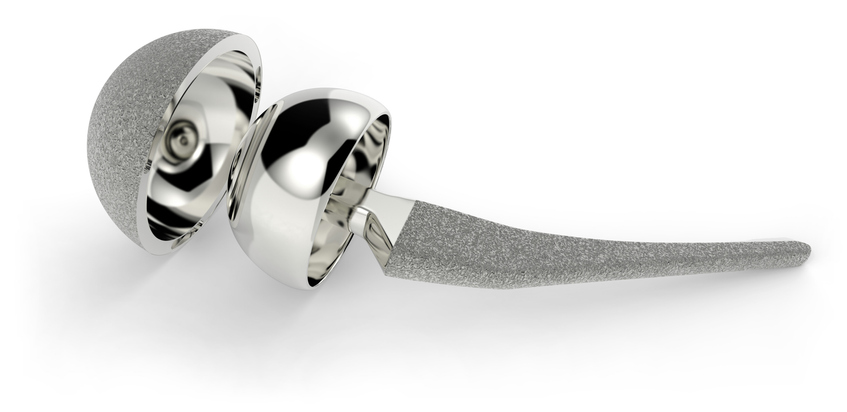
In the medical industry, precision in manufacturing is essential. Metal components that are used in medical devices, in particular, must meet exacting standards to ensure they perform safely and reliability, whether they’re part of life-saving equipment or tools used in daily procedures. For this purpose, fewer manufacturing methods rise to the occasion like CNC machining. Capable of delivering unmatched accuracy and consistency, CNC machining is uniquely positioned to meet the critical needs of medical component manufacturing.
An automated, computer-driven process, CNC machining can create intricate, high-precision components from biocompatible materials, all while meeting tolerances that other methods struggle to achieve. This advanced technology supports compliance with rigorous regulatory standards and opens up opportunities for innovation, from patient-specific implants to advanced surgical instruments. Let’s take a closer look at how CNC machining is reshaping medical manufacturing through precision and innovation.
How CNC Machining Transforms Medical Component Manufacturing
CNC machining has been instrumental in revolutionizing the medical component manufacturing industry. By enabling the production of highly complex, precise parts that meet strict specifications (many times down to microscopic tolerances), CNC machining ensures the quality necessary for advanced medical applications, including imaging devices and implantable parts.
Another key advantage of CNC machining is its adaptability for customization. This allows for patient-specific components, like custom-fitted implants and specialized surgical tools, that can be tailored to individual anatomical requirements to enhance comfort, functionality, and overall treatment outcomes. This flexibility has led to innovation like bespoke joint replacements and uniquely designed surgical instruments that improve procedural accuracy and patient care.
CNC machining also supports a range of materials that are uniquely suited to medical applications. Metals like titanium and stainless steel, for instance, offer strength and biocompatibility for implants. These types of materials allow CNC machining to meet the demands of different medical environments and applications, pushing the boundaries of what’s possible in healthcare technology.
Types of Medical Components Manufactured Using CNC Machining
CNC machining has become essential in medical component manufacturing. A number of components with unique demands for precision, durability, and biocompatibility are only possible as we know them because of this manufacturing process. For instance:
- Implants — High-precision implants rely on CNC machining to achieve the exact specifications needed for optimal integration with the body. Whether producing dental implants or orthopedic components, CNC machining ensures each implant meets strict tolerance and material requirements to enhance patient outcomes.
- Surgical Instruments — CNC machining plays a critical role in creating surgical tools that require exact accuracy and durability to withstand repeated sterilization and surgical use. From scalpels to forceps, CNC-machined instruments support the high standards needed in surgical environments, where precision can directly impact patient safety.
- Medical Device Parts — For components in devices like pacemakers and MRI machines, CNC machining provides the reliability and consistency needed for sensitive medical equipment. With CNC’s high precision, manufacturers can produce intricate parts that meet the stringent requirements of devices that must operate seamlessly within the human body and clinical settings.
- Prototyping for Medical Innovation — CNC machining also excels in rapid prototyping, allowing for the quick development and testing of new medical devices and components. This capability accelerates innovation, helping manufacturers bring next-generation medical solutions to market with greater speed and accuracy.
Benefits of CNC Machining in Medical Component Manufacturing
Precision and Accuracy
More than almost any other manufacturing method, CNC delivers the tight tolerances and exacting precision required for medical component manufacturing. This helps ensure that each part aligns with critical specifications, such as those in implants and surgical tools where even slight deviations can impact performance and patient safety.
Consistency and Repeatability
During high-volume manufacturing in particular, consistency is key. And CNC machining provides this in spades. When each batch of components must meet high standards, CNC machining is capable of producing high volumes of identical components repeatedly; this is essential for maintaining quality and reliability across large-scale production runs.
Speed and Efficiency
While other methods like additive manufacturing (i.e. 3D printing) can deliver the same high levels of precision and consistency, only CNC machining offers the trifecta of precision, consistency, and speed. CNC machining streamlines production by reducing lead times for faster turnaround — all without sacrificing quality. This efficiency allows manufacturers to bring components to market more quickly and at a more competitive cost, benefiting both producers and end-users.
Innovation-Driven Flexibility
And finally, CNC machining supports medical innovation by making it easier to create complex, custom designs. From intricate medical devices parts to uniquely tailored implants, the flexibility of CNC machining allows engineers and designers to explore new possibilities in medical technology and device design.
The Future of CNC Machining in Medical Manufacturing
Emerging technologies in CNC machining are poised to revolutionize the medical component manufacturing landscape further, pushing the boundaries of what’s possible in medical component production.
For instance, advancements like 5-axis CNC machines and automated processes have enhanced precision and efficiency in ways that were previously unattainable. And this is likely to continue. With multi-axis machining, manufacturers can produce increasingly complex geometries required for cutting-edge medical devices and implants — all while reducing setup time and ensuring consistent results.
As CNC machining technology continues to evolve, so will its role in medical breakthroughs. Precision-engineered components made possible by CNC machining can lead to more effective treatments, improved patient outcomes, and even reduced recovery times. And the flexibility and accuracy of this method will likely continue to open doors for innovations in personalized medicine, custom implants, and next-generation medical devices.
Advantage Metal Components Delivers Precision Medical Component Manufacturing
In medical component manufacturing, the need for precision, consistency, and innovation is paramount. CNC machining stands out as an essential process that enables the creation of reliable, high-precision components tailored to the rigorous demands of the medical industry. Whether producing surgical instruments, custom implants, or components for life-saving devices, CNC machining offers the necessary accuracy, material flexibility, and consistency required for this complex field.
As a trusted partner in advanced manufacturing, Advantage Metal Products brings a wealth of expertise, state-of-the-art equipment, and a commitment to quality to every project. We’re an ISO 13485-certified manufacturer. Our team in Livermore, CA, works closely with our medical clients, delivering the exceptional level of precision needed to meet regulatory standards and enhance patient care. Through customized support, rapid prototyping via our partnership with Megatech, and CNC machining capabilities, we are here to support the creation of safe, reliable, and innovative medical products.
Ready to discuss your next medical manufacturing project? Contact us today to learn how we can help.